Porosity in Welding: Identifying Common Issues and Implementing Finest Practices for Prevention
Porosity in welding is a pervasive concern that typically goes unnoticed up until it creates significant problems with the stability of welds. In this conversation, we will explore the key variables adding to porosity formation, examine its harmful effects on weld efficiency, and talk about the ideal methods that can be embraced to minimize porosity event in welding procedures.
Typical Reasons For Porosity
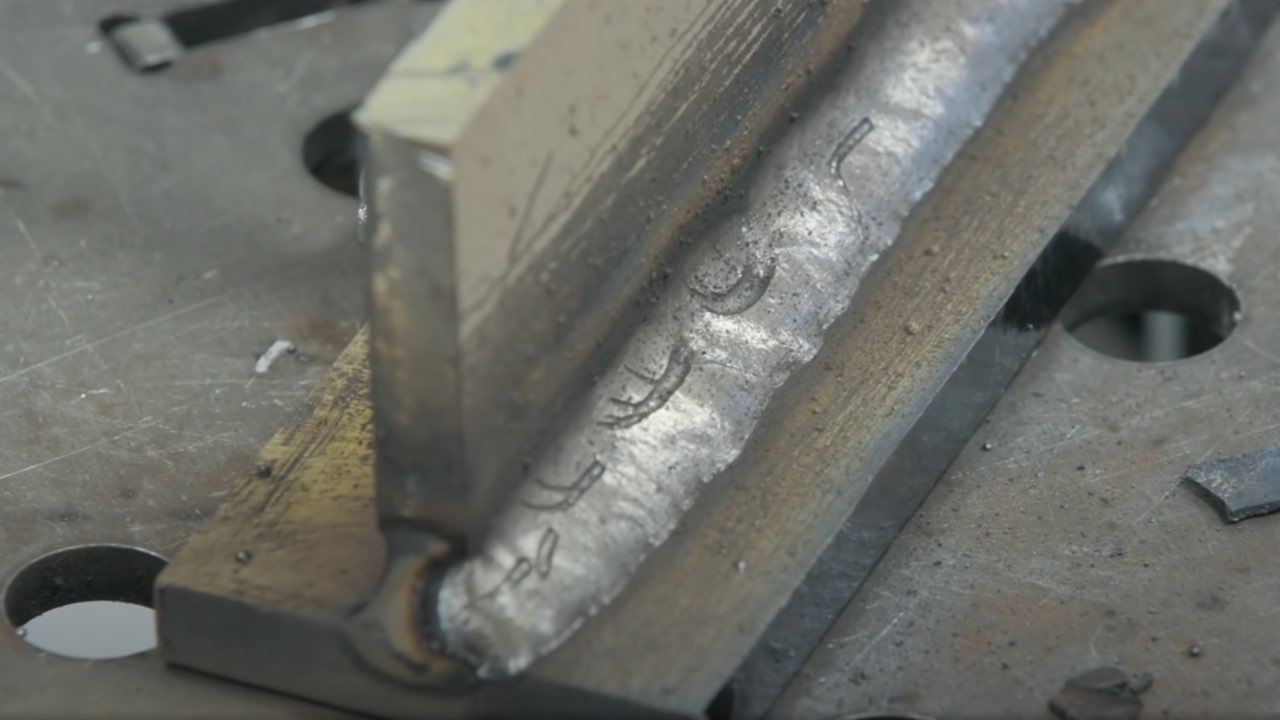
Using unclean or wet filler materials can present impurities into the weld, adding to porosity issues. To mitigate these usual causes of porosity, thorough cleansing of base steels, proper securing gas choice, and adherence to ideal welding specifications are vital methods in achieving high-grade, porosity-free welds.
Impact of Porosity on Weld High Quality

The existence of porosity in welding can substantially endanger the structural integrity and mechanical residential or commercial properties of bonded joints. Porosity develops gaps within the weld steel, deteriorating its total strength and load-bearing ability.
Welds with high porosity degrees often tend to show reduced influence strength and reduced capacity to warp plastically prior to fracturing. Porosity can hamper the weld's capacity to successfully transmit forces, leading to early weld failure and potential security dangers in essential structures.
Best Practices for Porosity Avoidance
To improve the structural integrity and quality of bonded joints, what particular measures can be executed to minimize the incident of porosity throughout the welding process? Porosity prevention in welding is critical to guarantee the honesty and toughness of the last weld. One efficient practice appertains cleansing of the base steel, getting rid of any kind of impurities such as rust, oil, paint, or dampness that could cause gas entrapment. Making certain that the welding devices is in great problem, with clean consumables and appropriate gas flow prices, can also significantly reduce porosity. In addition, maintaining a stable arc and controlling the welding parameters, such as voltage, existing, and take a trip rate, assists develop a consistent weld swimming pool that decreases the threat of gas entrapment. Using the correct welding technique for the certain product being welded, such as changing the welding angle and gun placement, can better avoid porosity. Regular evaluation of welds and instant removal of any type of concerns identified throughout the welding procedure are vital methods to stop porosity and create top notch welds.
Importance of Proper Welding Strategies
Implementing proper welding methods is critical in making sure the structural honesty and quality of welded joints, developing upon the foundation of reliable porosity prevention actions. Too much heat can lead to increased porosity due to the entrapment of gases in the weld swimming pool. Furthermore, utilizing the appropriate welding parameters, such as voltage, current, and travel rate, is essential for attaining audio welds with very little porosity.
In addition, the option of welding procedure, whether it be MIG, TIG, or stick welding, need to straighten see here with the details needs of the project to guarantee ideal outcomes. Correct cleaning and prep work of the base steel, as well as picking the appropriate reference filler product, are also crucial parts of proficient welding strategies. By sticking to these finest methods, welders can minimize the danger of porosity development and produce top notch, structurally audio welds.
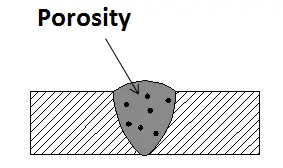
Examining and Quality Assurance Steps
Checking treatments are crucial to identify and stop porosity in welding, making certain the strength and toughness of the final product. Non-destructive testing approaches such as ultrasonic screening, radiographic screening, and aesthetic inspection are frequently employed to determine possible issues like porosity.
Post-weld assessments, on the other hand, assess the final weld for any type of issues, consisting you could try these out of porosity, and verify that it meets specified requirements. Carrying out a thorough high quality control strategy that includes comprehensive testing procedures and assessments is extremely important to decreasing porosity concerns and guaranteeing the general high quality of bonded joints.
Final Thought
In final thought, porosity in welding can be a typical issue that influences the quality of welds. By identifying the typical causes of porosity and executing ideal methods for prevention, such as correct welding strategies and screening steps, welders can ensure premium quality and trustworthy welds. It is important to prioritize avoidance approaches to lessen the event of porosity and maintain the stability of bonded frameworks.
Comments on “Understanding What is Porosity in Welding: Causes and Solutions”